Treatment Quality Monitoring (TQM)
Overview
The waste management process comprises five key stages: Generation, containment, transport, treatment, and reuse. To ensure effective waste management, each of these stages must receive adequate attention. Inadequate waste treatment and the subsequent discharge into the environment directly harm both the environment and water quality. Often, effluents find their way into surface water sources. The poor quality of wastewater effluents contributes to the deterioration of the receiving surface water bodies and poses risks to users' health.
Quality and reusability are intimately linked: Well-treated waste output can be repurposed, whether as recycled water or compost. Consumer acceptance of this practice largely hinges on the quality of the output and the benefits it offers.
At present, there is minimal visibility into the handling and treatment of waste at treatment plants. With this in mind, we are introducing Treatment Quality Monitoring (TQM) as an extension to DIGIT Sanitation.
Why do we need Treatment Quality Monitoring?
The vision of DIGIT Sanitation is “Zero untreated waste in 1,000 ULBs in 1000 days”. Read more about why this matters here.
To achieve “zero untreated waste” it is pertinent to ensure that waste is disposed of in the right method, right place, and right time. Subsequently, all waste disposed of should be processed and treated effectively. We can ensure that the waste is being effectively treated by focusing on the following:
Design the best process for waste treatment.
Ensure adherence to the designed process.
Monitor and track the effectiveness of the process.
We now explore each issue separately:
How do you know that the process you have designed is correct/needs modifications?
The success of a treatment will reflect directly in the results of the process, in terms of quality of output and process efficiency.
Testing at various stages of the process and comparing the parameters from the test results against a benchmark will be an indicator of an effective process.
Based on variations between {what the values should be in an ideal condition} and {the measured values} of the parameters, the changes required in each specific part of the process can be identified.
How do you ensure the process is being followed?
There are no digital touchpoints in the process, so there is no unbiased/people-independent method to track adherence.
An indirect method to measure adherence is through the “measure of outcomes” (parameter testing) and review of the process based on the results thereby leading to the detection of deviations from the SOP.
How do you assess if the process is effective?
Test the treated output at various stages and check if all test parameters are within acceptable range as per standards
Based on the above, monitoring parameters is a key step in ensuring waste is treated and disposed of properly.
Key Problems:
Treatment quality monitoring (TQM) is not being carried out in most urban local bodies (ULBs).
Test data is not recorded/analysed for process improvements.
No digital touchpoints in the TQM lifecycle: Lack of such touchpoints create data silos that hinder the relevant information from being accessible to the right person at the right time.
No accountability system in place to assign responsibility to stakeholders to make necessary changes.
TQM is dependent on having access to a lab and also the logistics of sample collection, transportation, interpersonal communications, and waiting times (for tests/test results).
To address these issues, we want to introduce a product for Treatment Quality Monitoring. The objective is to improve the quality of treated waste.
Approach
Our hypothesis of how treatment quality can be improved is as follows:
Configure Treatment Processes and Testing Requirements: Configuration of plants and treatment processes provides a consolidated view to the state/TSUs/stakeholders of the treatment processes operational at plants. Additionally, this allows for the definition of treatment requirements, frequencies, and benchmarks at the state level for various processes and their adoption by plants.
Ensure Regular Testing: Implementing regular and high-frequency testing enables the early detection of deviations from the established benchmarks.
Quick Issue Resolution: Identifying deviations and diagnosing them through an analysis of both current and historical data facilitates rapid issue resolution.
Deepen Enquiry: Is a particular plant consistently performing badly? Is a particular treatment process regularly leading to poor-quality output? Which step in the process flow is the deviation starting from? Do quality test results fluctuate often? Looking at trends in data can help deepen enquiry and identify problem areas.
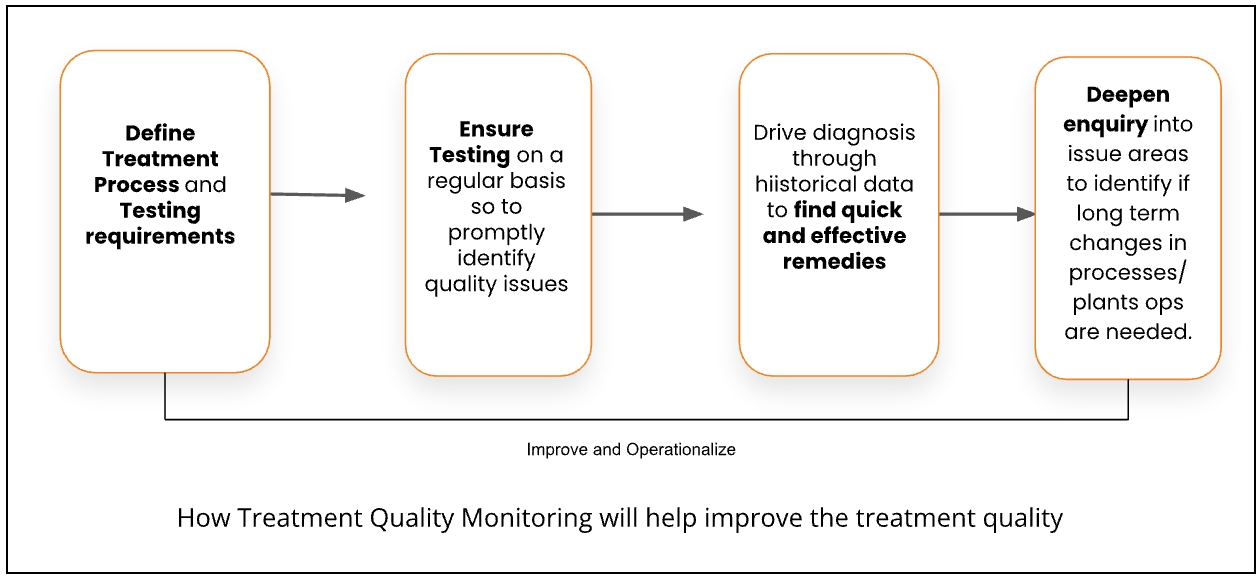
Goals of Treatment Quality Monitoring
Goal
How will it be measured via the product?
How will we know TQM is successful?
To ensure treated waste is as per quality standards.
The percentage of plants with output quality as per benchmarks.
Increase in the percentage of plants with output quality as per benchmarks over time
To ensure treated waste is tested regularly for quick identification of issues.
The percentage compliance against the testing schedule.
Increase in the percentage compliance against the testing schedule over time.
Value Bundles
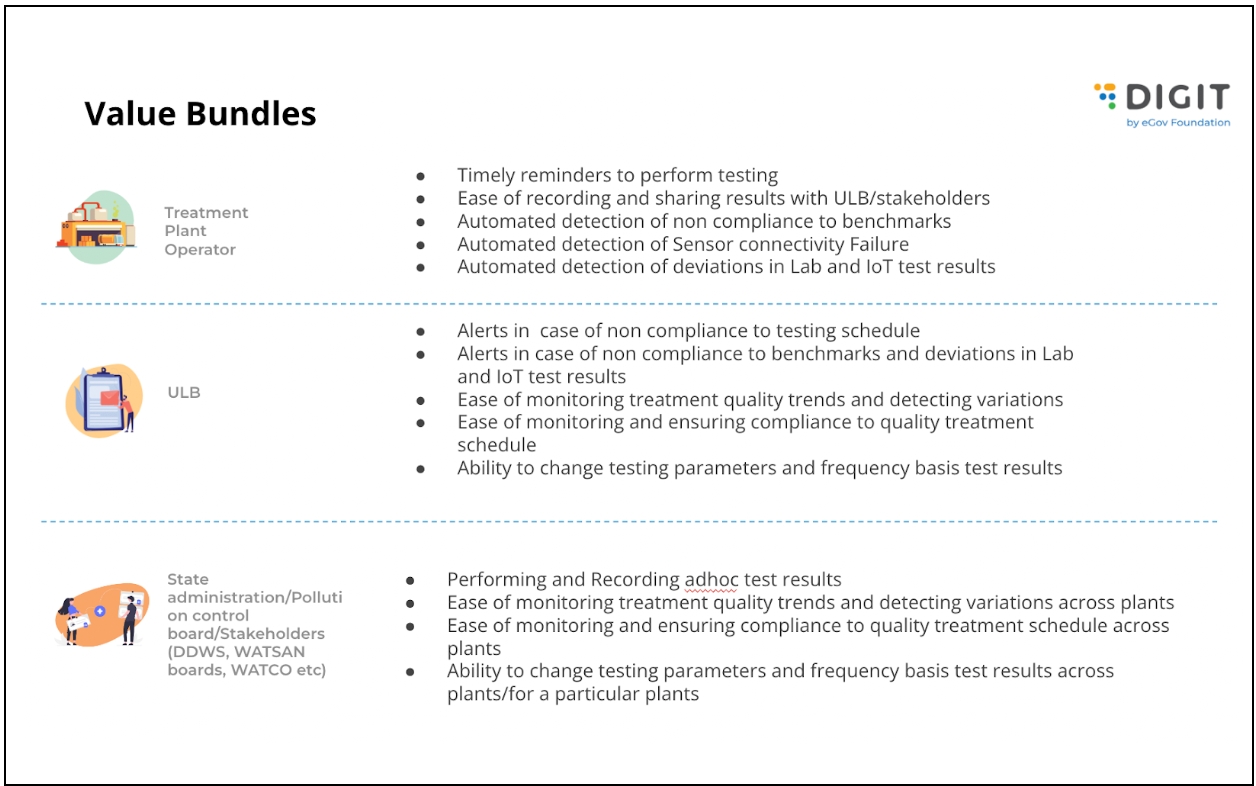
Was this helpful?